Our production process from start to finish
The Pampa Camarones Cathode Plant is designed to process 60,000 tons/month of ore, which is crushed and later stored in piles, on which an irrigation system is incorporated for leaching. The solutions obtained are handled through accumulation pools, being entered into the Plant for processing, in order to produce, via electrowinning, 700 t/month (8,400 tons/year) of copper cathodes. The ore already leached in the heaps,
is transported to the rubble dump for its final disposal.
The Pampa Camarones Cathode Plant Project considers the electrical supply through a 23 kV electrical transmission line. While the water supply was considered through a seawater adduction pipe.
Operations
Crushing Plant
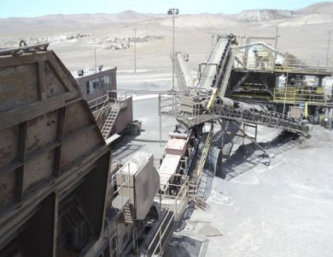
This section is in charge of delivering the ore from the mine duly crushed to a uniform granulometry to the leaching piles. It consists of a primary jaw crusher, a cone crusher that acts as a secondary crusher, and an agglomerator drum. Each of these units is fed by hoppers, conveyor belts and screens designed for this purpose.
Heap Leaching
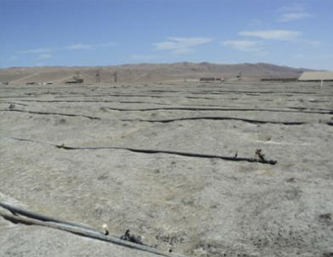
In this section, the agglomerated ore from the crushing area is placed in leach pads of an average height of 2.5 to 3.0 meters which are irrigated with solutions acidulated with sulfuric acid for a period of 90 days. In this period an average recovery of 82.7% of the CuT is obtained. The irrigation can be done with drippers or sprinklers. The solutions depending on their concentration are directed to the different operation ponds.
Solvent Extraction (SX)
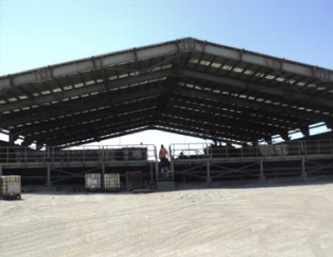
The installation includes an operation circuit consisting of a copper-rich aqueous solution pond called PLS, an organic regulator tank, six mixer-settling tanks (E1, E2, E3, L1, L2 and S1), two post-decantation ponds of refine and a treatment system of waste from the operation of the plant.
Electro winning (EW)
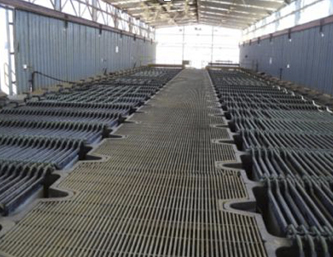
The Electro winning (EW) plant is equipped with 50 cells of polymer concrete, divided into 2 sections with 25 cells each, arranged in a back-to-back configuration. The cells are electrically connected in series, containing 31 cathodes and 32 anodes each, at a distance of 100 mm between cathodes. The electrodes used are permanent 316L stainless steel cathodes and insoluble anodes Pb-Ca-Sn alloy. The electric direct current supplied to the plant is through two identical rectifiers 12,000 [A] each, connected in parallel, having a total available of 24,000 [A] for the operation. The final product obtained, Cu cathodes, are packaged in bundles and sold.